-
Designed to meet the high precision demands of cutting-edge industries, Dah Bah’s Copper Foil Slitting Machine combines advanced automation with exceptional reliability. Below, we explore the key features that make it a top performer across a wide range of applications, including those involving anode material processing.
Performance and Precision Control
-
Individual Motor-Driven Rollers
Each roller is equipped with its own motor, allowing for independent control of speed and torque. This precise synchronization ensures smooth material flow, even at high speeds, significantly reducing slippage, misalignment, and material waste. This is particularly important when handling delicate copper foil used as a substrate for anode material in battery manufacturing.
-
Special Roller Surface Treatment
Our rollers undergo a unique surface treatment designed to protect delicate copper foil from damage and contamination. This treatment not only preserves material integrity but also enhances grip, ensuring consistent tension control for accurate slitting.
-
Nip Rollers with Adjustable Gap
The nip rollers are designed with an adjustable gap, allowing operators to fine-tune the pressure according to the material thickness. This feature ensures smooth feeding, helping to prevent issues such as stretching or wrinkling of the copper foil.
-
High-Precision Shear Cutter with Alignment Device
The shear cutter delivers precise cuts, slicing the material into narrow strips without damaging the edges. An integrated alignment device ensures the cutter stays perfectly positioned, resulting in straight, accurate cuts across the entire length of the roll.
Optimized Rewinding and Material Management
-
Efficient Rewinding System
Our rewind contact roller maintains even tension during the rewinding process, ensuring consistent product quality. The system also includes a roll-weighting mechanism that accurately measures rewind rolls, promoting optimal material management and minimizing waste.
-
Coreless Trim Rewinding
The coreless trimmed waste rewinding stand efficiently collects excess material without using a core, making it easy to dispose of or recycle. A trim rewinder pusher automatically removes the trimmed waste after rewinding, reducing downtime and ensuring a seamless operation.
Advanced Automation and Drive System
-
Siemens PLC Control and Drive System
The Siemens PLC (Programmable Logic Controller) system automates the entire machine, coordinating each component for smooth and efficient performance. Independent motor control for each roller allows for precise speed and tension adjustments, ensuring consistent material flow from start to finish, even at high speeds.
With its cutting-edge design and optimized performance, Dah Bah’s Copper Foil Slitting Machine delivers reliable, precise, and user-friendly operation tailored to the needs of high-tech industries. Whether you're working with copper-clad laminates, circuit boards, microchip substrates, or anode material for lithium-ion batteries, this machine plays a crucial role in producing the essential materials that power modern technologies. Its versatility makes it an excellent choice for industries like consumer electronics, mobile devices, energy storage systems, and electric vehicles.
Ready to enhance your production capabilities? Contact us today to learn how our Copper Foil Slitting Machine can help you achieve your production goals.
-
Model No. | SLS-ET150HI |
---|---|
Applicable Material | Copper foil 6-35μ |
Tension Range | 10-30 Kg 15-60 Kg for unwinder and 15-60 Kg for rewinder |
Parent-web Width | 1060-1480 mm |
Parent-web Diameter | φ550 mm |
Slitting Width | 200-1260 mm |
Maximum Finish-roll Diameter | φ550 mm |
Unwinding Core Inner Diameter | As required |
Rewinding Core Inner Diameter | φ3" & φ6" |
Machine Speed | 5-150 M / min. |
Machine Color | White |
Power Supply | As required |
*The working speed depends on the material condition and slitting width.
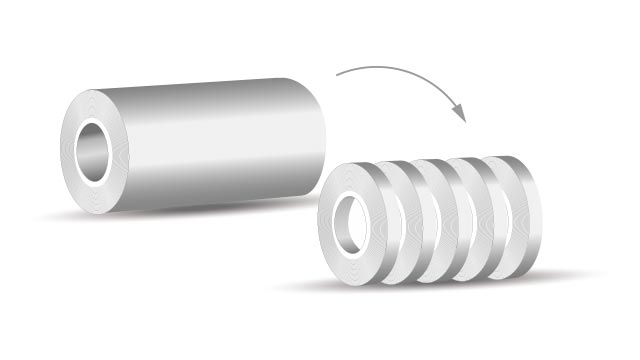
Copper
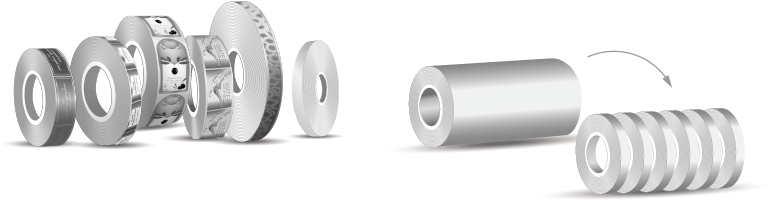